Лекция 3
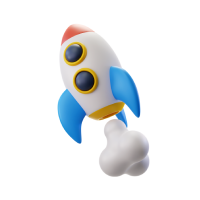
Лекция 3
1. Лекция 3. Вторичные процессы перегонки нефти. Технология термических процессов переработки нефтяного сырья
Технологические параметры процесса. Термодинамика и кинетика диктуют следующие условия проведения пиролиза: ––быстрый подвод значительного количества тепла; ––снижение парциального давления углеводородов; ––минимальное время контакта; ––минимальное время охлаждения газов пиролиза, выходящих из реактора, для предотвращения нежелательной полимеризации олефинов.
Как известно пиролиз сырья осуществляется в змеевиках трубчатых печей при температуре 700-1000°С. Важнейший параметр процесса – температура – фактор, определяющий как степень разложения исходного вещества, так и распределение продуктов пиролиза. С увеличением температуры до 900оС повышаются выходы низших олефинов, метана и водорода и снижается выход алканов.
Другим важным параметром пиролиза является время пребывания (время контакта) пиролизуемых веществ в зоне реакции. Выход водорода и метана с увеличением времени пребывания непрерывно возрастают. Выход же этилена и некоторых других продуктов в зависимости от времени пребывания проходят через максимумы, характерные для каждой температуры в реакторе. Таким образом, увеличение температуры пиролиза с одновременным соответствующим сокращением времени пребывания способствует достижению более высоких выходов целевых продуктов, в том числе этилена.
Существенное влияние на результаты пиролиза оказывает профиль распределения температур реагирующих продуктов по длине реакционного змеевика. Более интенсивный нагрев сырья в начале змеевика приводит к возрастанию выходов этилена, а при более интенсивном нагреве в конце увеличивается выход пропилена, бутенов, бутадиена 1-3, ароматических углеводородов и снижается выход этилена.
Важным фактором, влияющим на селективность пиролиза, является давление в зоне реакции, точнее – парциальное давление углеводородной части реагирующего потока. Этилен и другие низшие олефины образуются в результате первичных реакций первого кинетического порядка. Степень превращения сырья по этим реакциям от давления не зависит, но олефины реагируют дальше, превращаясь в продукты полимеризации или конденсации и степень их превращения по этим направлениям пропорциональна парциальному давлению. Снижение давления на выходе из реактора благоприятно влияет на выходы олефинов С4 и бутадиена 1-3. Выход этилена меняется мало, а выход метана снижается. Расчёты показывают, что оптимальное давление на выходе из реактора в среднем находится в пределах 160-200 кПа.
Парциальное давление углеводородов в зоне реакции зависит также от перепада давления в потоке по длине реактора, который в свою очередь зависит от расхода сырья и его физических свойств, размеров и конструкции реактора. Относительно лёгким и часто применяемым способом понижения парциального давления является разбавление углеводородного сырья водяным паром. С увеличением разбавления углеводородов водяным паром снижается коксообразование в реакторе. В то же время увеличение разбавления сырья паром приводит при равном расходе сырья к увеличению капитальных вложений в отделение печей пиролиза и закалочного охлаждения, расхода топлива на печи пиролиза. Таким образом, от выбора конструкции реактора и режима в нём, обеспечивающего жёсткость и достаточную селективность зависят, как выходы целевых продуктов, так и экономические показатели работы всей установки.
Современные тенденции развития процесса пиролиза. Методы снижения потребления топливно-энергетических ресурсов на установке
К настоящему времени единственным освоенным и широко распространенным промышленным методом является пиролиз в трубчатых печах. Его качественное развитие направлено пока в основном по пути совершенствования существующей технологии. Однако, несмотря на достигнутый прогресс, связанный с изменением конструкции змеевика и конвекционной зоны печи, использованием современные закалочно-испарительных аппаратов (ЗИА), возможности этого процесса ограничены, особенно при использовании сырья, склонного к повышенному коксообразованию. Первые печи пиролиза первоначально ничем не отличались от нагревательных печей нефтезаводских установок. Они имели два потока, змеевик был выполнен в виде настенного экрана. Это не могло обеспечить высокую теплонапряжённость поверхности труб из-за большой неравномерности подвода тепла. Кроме того, топливо в таких печах сжигалось в факельных горелках, при этом создавалось неуправляемое распределение температуры внутри печи, в результате чего возникали частые пережоги труб даже при невысоких температурах пиролиза. Для таких печей температура на выходе не превышала 720- 760°С, коэффициент теплопередачи внутри змеевика 650-750 Вт/(м2·К), а время пребывания потока составляло 2-3 с. В таких печах пиролизу подвергали, как правило, этан и другие углеводородные газы. Для того чтобы перейти на жидкое сырьё, необходимо было упорядочить сжигание топлива в печи. С этой целью были разработаны панельные горелки беспламенного горения, которые могут создавать сплошную излучающую поверхность. При размещении змеевика в середине топочной камеры на подвесках («ёлочках») удалось повысить коэффициент теплоотдачи в змеевике до 950-1050 Вт/(м2·К), однако время пребывания потока оставалось довольно большим 1,2-1,6 с. Для того чтобы снизить время пребывания потока в змеевике и повысить теплонапряжённость, начали использовать трубы изготовленные методом центробежного литья из более жаростойких сталей (Х25Н20, Х25Н35). Поскольку эти трубы более хрупкие, то от горизонтальных змеевиков перешли к вертикальным, свободно висящим змеевикам (так же при вертикальном расположении труб практически нет застойных зон). Такую конструкцию змеевиков имеет печь SRT-I разработанная фирмой «Lummus». Змеевики печи SRT-I расположены однорядно в сравнительно узкой топочной камере, выше которой находится секционная конвекционная зона. Всего в топочной камере располагается 4 змеевика, выходы из которых попарно соединены для подачи пирогаза в ЗИА. В таких печах пиролизу подвергают как бензиновые фракции, так и рецикловый этан при температуре около 830°С. Перепад давления в змеевике составляет около 0,15 МПа, время пребывания потока в нём около 0,75с. Средняя теплонапряжённость 80000 Вт/м2.
Перспективные способы пиролиза. Необходимость расширения сырьевой базы, сокращения удельного расхода сырья, а также энергетических и материальных затрат заставляет вести поиск новых модификаций процесса, в основном рассчитанных на пиролиз тяжелых видов углеводородного сырья (мазут, вакуумный газойль, нефть).
К числу таких процессов относят в первую очередь: – пиролиз в присутствии гетерогенных катализаторов (каталитический пиролиз); – высокотемпературный пиролиз с использованием газообразных теплоносителей (водяного пара, дымового газа, водорода); – пиролиз в присутствии инициирующих добавок, гидропиролиз; – пиролиз в расплаве металлов и их солей; – термоконтактные процессы.
В ходе разработки каталитического пиролиза исследовано влияние большого числа гетерогенных и гомогенных катализаторов. В условиях гетерогенно-каталитического пиролиза происходит увеличение селективности процесса и степени превращения сырья (выхода этилена). Результаты многочисленных работ, выполненных ими, позволили выявить каталитическую активность ряда соединений: оксидов металлов переменной валентности, оксидов и алюминатов щелочных, щелочноземельных и редкоземельных металлов, а также некоторых алюмосиликатов. Обычно их наносят на носители, в качестве которых применяют пемзу, модификации оксидов алюминия и циркония, корунд, аморфные и кристаллические цеолиты. Так, например, применение ванадата калия (KVO3) на синтетическом корунде, оксидов индия и калия на пемзе позволяет почти на 10% увеличить выход этилена по сравнению с результатами термического пиролиза высокой жесткости при сохранении выхода пропилена на прежнем уровне. Процесс каталитического пиролиза осуществляют в обогреваемых вертикальных трубах печей специальной конструкции. Варьируя состав катализатора, можно значительно изменять выход бутадиена. На отдельных катализаторах было исследовано влияние природы сырья, а при пиролизе индивидуальных олефинов высказаны предположения о возможных вариантах механизма каталитического пиролиза. Установлена специфическая роль водяного пара, взаимодействующего с поверхностью катализаторов. На опытных установках проведено исследование влияния коксообразования на каталитическую активность и отработаны условия регенерации катализатора, способного работать до 200ч (количество водяного пара около 75% по массе). Расчеты показали высокую эффективность каталитического пиролиза, приводящего к снижению на 10-12% себестоимости низших олефинов. В настоящее время центр исследований этого направления из России перемещается в Японию. В 1995 году там начата разработка нового проекта энергосберегающего способа получения этилена из нефти низкотемпературным каталитическим пиролизом с целью замены традиционного энергоемкого процесса. Полагая, что на его создание потребуется 10 лет, стоимость предстоящих работ оценили в 192 млн. долларов. Основой разработки остается выбор катализатора, отвечающего совокупности всех требований процесса. Переход от существующей технологии к каталитическому пиролизу позволит сэкономить 200 тыс. м3 топлива (30% энергозатрат) на 1 млн. тонн этилена.
В качестве гомогенных инициаторов первичных реакций пиролиза был исследован широкий круг соединений. Целью их применения являлось снижение жесткости процесса при сохранении (увеличении) селективности и выхода по этилену. По различным причинам одни из самых активных инициаторов – пероксид водорода (высокая стоимость добавки) и хлороводородная кислота (проблемы коррозии) не получили практического применеия. Отмечено положительное влияние некоторых кислородсодержащих органических соединений (кислоты, спирты, отходы различных производств, содержащие смеси этих и других окисленных углеводородов) на выход этилена, возрастающее с “утяжелением” исходного сырья. Для уменьшения скоростей вторичных реакций и увеличения скорости газификации откладывающегося кокса в качестве добавок предложено применять органические и неорганические соединения S и Р, соли и гидроксиды некоторых металлов. К синергетическому эффекту (увеличение скорости и снижение коксообразования) приводит использование в качестве активизирующей добавки продуктов озонолиза определенных нефтепродуктов, включающих одновременно и серо- и кислородсодержащие фрагменты.
Другое направление — гидропиролиз, заключающийся в замене части водяного пара водородом. Роль водорода заключается в образовании радикалов •Н по реакции • • 14) СНЗ+ H2 ↔ CH4+ Н Радикал •СН3 замещается более активным радикалом •Н. С реакцией (14) конкурирует реакция: • • 15) СН3+ RH ↔ СН4+ R. Поэтому концентрация молекулярного водорода должна быть достаточно высокой. За счет реакции (13) при гидропиролизе возрастает выход этилена и снижается выход пропилена. Кроме положительного влияния на скорость первичных реакций присутствие Н2 снижает степень коксообразования. Недостатки варианта гидропиролиза связаны с дополнительным расходом водорода и увеличением объема газообразных продуктов пиролиза, что приводит к ухудшению показателей стадии разделения пирогаза. С целью их устранения был предложен вариант поведения пиролиза в условиях повышенного давления водорода –– 2,0-2,5 МПа. При повышении давления водорода возрастает выход этана, а выход этилена за счет этого уменьшается. В жестких условиях при пиролизе бензинов выход этилена составляет около 40%, метана – 34%. Аналогичные результаты получены при подаче в зону пиролиза нафты или газойля водородсодержащих продуктов предварительно проведенного пиролиза этана. Термоконтактный пиролиз возможен с использованием жидких, газообразных и твердых теплоносителей. Применение же для этой цели расплавов: (некоторых металлов (свинец, висмут, кадмий, олово и др.) и их сплавов, солей (хлоридов, карбонатов и др.), а также шлаковых (оксидных) расплавов) имеет ряд достоинств. К ним относятся: высокоэффективная теплопередача, возможность переработки практически любых видов сырья, простота непрерывной эвакуации сажи и кокса из зоны реакции. Пиролиз в расплавах позволяет получать из широких нефтяных фракций этилен с высоким выходом (до 25% при пиролизе нефти). Значительный комплекс работ в этом направлении с изучением различных способов технологического оформления процесса выполнен советскими учеными. Исследованы различные способы контактирования углеводородов с теплоносителем: барботаж через слой расплава, переработка в дисперсии или пленке расплава. По способу подвода тепла возможен прямой контакт расплава со средой либо через стенку аналогично процессу пиролиза в трубчатых печах. Основные проблемы пиролиза в расплавах связаны с необходимостью нагрева и циркуляции теплоносителя. С целью их решения проверен вариант пиролиза в трубчатых печах с дисперсионно-кольцевым течением расплава. За счет повышения теплонапряженности поверхности змеевика удалось значительно сократить его длину, а значит, и время пребывания в нем сырья до 0,05 с. Соответственно наблюдали и увеличение выхода этилена при пиролизе бензина с 28 до 41%. Применение расплавов металлов с температурой плавления стью 100 тыс. тонн по перерабатываемой нефти. Дальнейшим развитием технологии этого процесса занимался консорциум японских фирм и “Union Carbide”. Мощность опытных установок была доведена до 2000 т этилена в год, но запланированные сроки промышленной реализации проекта все время отодвигаются. Аналогична судьба и русского аналога, применявшего в качестве теплоносителя смесь водяного пара и водорода и предназначенного для пиролиза вакуумного газойля и мазута. Появление перспективных вариантов каталитического, инициированного, водородного пиролиза пока не привело к кардинальному пересмотру сложившихся представлений. Зато достигнут значительный прогресс на стадии разделения, в результате которого стали доступными индивидуальные бутены, изо- и н-амилены, изопрен, дициклопентадиен, что может дать резкий толчок к развитию новых промышленных синтезов на их основе. Расширение сырьевой базы и спектра продуктов пиролиза, согласно большинству прогнозов, сохранит за ним ключевые позиции в нефтехимии и в реально обозримом будущем.
Среди термических процессов в нашей стране и за рубежом получил процесс замедленного коксования, который позволяет перерабатывать самые различные виды тяжелых нефтяных остатков с выработкой продуктов, находящих применение в различных отраслях.
Коксование — это термический крекинг тяжелого
нефтяного сырья в более жестких условиях, при котором в качестве одного из
продуктов получается твердый остаток — кокс. После многих лет накопления
информации о термическом крекинге стало достаточно ясно, что благодаря высоким
температурам и очень высоким скоростям подачи сырья, коксообразования не
происходит, пока сырье не выходит из узких змеевиков в печах в большой уравни
тельный резервуар. Если углеводородную
смесь задержать в этой изолированной емкости, которая называется коксовый
барабан, то можно провести управляемые процессы глубокого крекинга и
коксования. Была разработана технология, которая позволяет эффективно проводить
этот процесс, включив его в непрерывный режим крекинга. Хотя идея коксования
проще, чем идея крекинга, в первом случае требуется более сложное оборудование,
так как приходится иметь дело с коксом. Поскольку кокс — твердое вещество, то
возникают дополнительные проблемы. Сырье для коксования (то же, что и для
крекинга) нагревают приблизительно до 540°С (~1000°F) и подают в нижнюю часть
коксового барабана. Легкокипящие продукты крекинга поднимаются вверх и
откачиваются из верхней части барабана. Высококипящие продукты остаются и,
поскольку нагревание продолжается, разлагаются до кокса, который представляет
собой твердое вещество, похожее на уголь. Пары из верхней части барабана
направляют на ректификацию, так же, как и продукты термического крекинга.
Удаление кокса из барабана — отдельная проблема, так как он представляет собой
твердую лепешку. В прежние времена реактор термического крекинга иногда
закоксовывался в результате какого-либо нарушения технологического режима или
аварии. Единственным способом вычистить кокс из реактора было послать туда
рабочих в кислородных масках с отбойными молотками. Несомненно, что именно это
сдерживало разработку производства кокса на нефтеперерабатывающих заводах.В
настоящее время удаление кокса — это ежедневная рутинная процедура, которая
осуществляется подачей струи воды под давлением (около 2000 psi или 140 атм).
Выходы. Продукты, выходящие с установок коксования и термического крекинга, чувствительны к условиям процесса, к которым прежде всего относятся температура в печах и свойства сырья. Область температур кипения, групповой состав и относительная плотность сырья обычно позволяют предсказать результаты процесса. В качестве примера рассмотрим результаты переработки остатка с установки вакуумной перегонки (полученного из Западно-Техасской сырой нефти) на установке термического крекинга, работающей в режиме максимального производства бензина, и на установке коксования.
Таким образом, при термическом крекинге количество остатка уменьшается на 80%. В случае коксования остатка вообще нет, но образуется около 30% кокса, для которого нужен рынок сбыта. В обоих процессах образуются также бензин, нафта и газойль, но они низкого качества. Нафту часто перерабатывают на установке каталитического риформинга, а газойль — на установке гидрокрекинга.
Кокс. О коксе полезно сказать несколько слов. Большая часть кокса, который выпускается нефтеперерабатывающим заводом, выглядит как губка и потому называется губчатый кокс. Основные области применения такого кокса — это производство электродов, получение карбида кальция и графита. Прочность губчатого кокса недостаточна для его использования в доменных печах для выплавки чугуна или в литейном производстве.
Вторая форма кокса — игольчатый кокс, который так называется из-за своих удлиненных микрокристаллов. Чтобы получить такой кокс, требуется особое сырье и более жесткие условия работы. По своему качеству такой вид кокса предпочтительнее в производстве электродов, чем губчатый кокс. В результате, игольчатый кокс значительно дороже, чем губчатый. Кокс содержит некоторые количества воды и жидких углеводородов, поэтому перед использованием он должен быть высушен. Измельчение кокса с последующим нагреванием с целью удаления этих примесей называется кальцинированием.
Кроме того, кокс можно применять в качестве топлива на нефтеперерабатывающем заводе — точно таким же образом, как используется любое другое твердое топливо, например, каменный уголь.