Лекция 7
Сайт: | Satbayev University - Институт дистанционного обучения |
Курс: | Промышленный катализ / Айткалиева Гульзат Сляшевна |
Книга: | Лекция 7 |
Напечатано:: | Гость |
Дата: | суббота, 5 июля 2025, 11:59 |
1. Лекция №7. Задачи и основные катализаторы процесса изомеризации
Процесс изомеризации лёгких бензиновых фракций связан с наличием водорода в реакционной среде. Вовлечение водорода в процесс регулируется специально вводимым в катализаторы металлическим компонентом. В качестве металлического компонента бифункциональных катализаторов на основе анионмодифицированных оксидов традиционно используются платина, палладий, никель, а также ряд других, дополнительно их модифицирующих переходных металлов. Оптимальное содержание металлов в катализаторах может составлять 0,1-1,0 % (мас.). При синтезе в качестве предшественника платины в основном используют гексахлороплатиноводородную кислоту. Для введения палладия применяют его хлорид. Никельсодержащие катализаторы чаще всего получают с использованием нитратной соли. На заключительных стадиях модифицирования проводят повторное прокаливание и обработку катализаторов в атмосфере водорода.
В высокотемпературных процессах риформинга и изомеризации углеводородов, протекающих на системах Pt/F - /Al2O3 и Pt/Cl- /Al2O3при температурах 350—500 °С, на основных стадиях превращения углеводородов происходит их дегидрирование на дисперсных металлических частицах, а кислотные функции носителя лишь промотируют протекание целевых реакций. Гидрирование ненасыщенных углеводородов, осуществляемое в термодинамически благоприятной области низких температур, также в основном обусловливается присутствием в составе катализатора металла.
Для низко- и среднетемпературных катализаторов изомеризации алканов, в которых металлический компонент - платина - распределен по поверхности сильнокислотной матрицы типа Al2O3/Cl- или ZrO2/SO4 2- , определяющими их активность являются уже кислотные свойства. В этом случае функции металла сводятся к активации водорода и к донированию в реакционную систему частиц Н+ и Н- . Гидрид-ионы, генерируемые из молекулярного водорода, обеспечивают повышенную скорость насыщения изоалкильных катионов на кислотных центрах, способствуя быстрой десорбции молекул изоалканов и сводя к минимуму их вторичные превращения по пути крекинга и олигомеризации.
Модификация оксида. Модифицированию могут подвергаться как непосредственно оксид металла, так и его гидроксидный предшественник.
Возникновение бренстедовской кислотности при формировании анионмодифицированных оксидов металлов обусловлено реакцией нейтрализации части основных гидроксильных групп на поверхности оксида и образованием связи между катионом металла и модифицирующим анионом
Наличие бренстедовских кислотных центров (БКЦ), связанных с терминальными и мостиковыми группами М-ОН установлено также для сульфатсодержащих оксидов алюминия, титана, циркония. Кроме того, для сульфатированных оксидов титана и циркония предполагают возникновение дополнительного типа протона, делокализованного между атомами кислорода группы 2 SO4 - и кислородом ближайшей группы М-ОН.
Помимо этого, сульфатирование и последующее прокаливание приводят к формированию льюисовских кислотных центров (ЛКЦ), представленных координационно ненасыщенными катионами алюминия, титана и циркония.
Фторид-ионы обычно вводятся из растворов фтористоводородной кислоты или фторида аммония на стадии приготовления гидроксида или оксида с последующим закреплением F -при прокаливании (500 °С). Наиболее высокое количество БКЦ имеет модифицированный оксид с содержанием фтора 1 % (мас.).
В случае введения фтора в гидроксидный предшественник максимальную кислотность приобретают катализаторы, содержащие 3-4 % (мас.) фтора.
Первые версии катализаторов риформинга готовили на основе фторированных алюмооксидных носителей с содержанием фтора 0,3-0,4 % (мас.), что обеспечивало оптимальное соотношение между реакциями ароматизации и гидрокрекинга углеводородов.
Фтор прочно связывается с оксидом алюминия и поэтому фторированный оксид алюминия может быть достаточно стабилен в гидротермальных условиях. Это позволяло использовать его в ранних вариантах процессов риформинга и изомеризации, не предполагавших осушку исходного сырья. Более того, катализаторы на основе F - /Al2O3 могут работать и в среде водяного пара, например, при скелетной изомеризации н-бутенов.
Что касается хлорированного оксида алюминия, то использование его дня получения катализаторов риформинга и изомеризации углеводородов стало возможным после введения в технологии этих процессов систем сорбционной осушки. Оптимальным считается содержание хлора в катализаторе риформинга 0,8-1,0 % (мас.). К преимуществам хлорсодержащих катализаторов относятся более высокая активность, а главное, возможность дозирования содержания хлора на поверхности носителя катализатора и, следовательно, его кислотной функции, непосредственно в ходе эксплуатации путем варьирования подачи хлорирующих и гидролизующих агентов. Сильнокислотные галоген содержащие системы получаются при газофазном фторировании или хлорировании оксида алюминия с использованием галогензамещенных углеводородов (CF4, СС14 и др.). Начиная с 1960-х годов и по настоящее время катализаторы на основе хлорированного оксида алюминия, содержащие до 16 % (мас.) хлора, остаются наиболее активными и селективными катализаторами изомеризации прямогонных бензиновых фракций.
Изомеризация пентан-гексановых фракций для получения высокооктанового компонента автомобильного бензина.
Процесс изомеризации пентан-гексановой фракции является одним из самых эффективных способов получения высокооктановых компонентов бензинов с улучшенными экологическими свойствами.
Изомеризация бензиновых фракций является неотъемлемой частью производства автомобильного бензина по требованиям высоких экологических стандартов и получила распространение в нефтехимии для получения индивидуальных алканов.
Технология Изомалк-2 получила признание благодаря сочетанию технологической эффективности, экономии энергоресурсов и отсутствию вредных выбросов.
Преимущества технологии Изомалк-2
1. Низкие температуры процесса обеспечивают протекание реакций изомеризации в термодинамически благоприятных условиях. Минимальный уровень крекинга в процессе обеспечивает выход целевого продукта до 99% масс. на сырьё.
2. Изомеризация пентана происходит без подачи реагентов. Отсутствует коррозия технологического оборудования. Отсутствуют технологические отходы и выбросы, требующие утилизации. В продукте отсутствуют микропримеси хлора, серы.
3. Минимальные эксплуатационные затраты.
4. Высокая надежность каталитической системы. Срок службы катализатора СИ-2 – более 12 лет, временное повышение примесей в сырье не приводит к безвозвратной потере активности катализатора.
5. Катализатор не требует регенераций и перегрузок в течение всего срока службы.
Процесс изомеризации с минимальными эксплуатационными затратами
1. Температура на входе в реакторы в процессе Изомалк-2 остаётся низкой (120-140°С) в течение всего срока службы катализатора с обеспечением исчерпывающей глубины изомеризации.
2. Высокая активность катализатора в реакциях изомеризации пентан-гексановой фракции позволяет уменьшить количество рецикла в схемах с рециркуляцией.
3. Устойчивость к действию каталитических ядов не требует специальной доочистки сырья от примесей серы и азота, как в схемах с хлорированными катализаторами.
4. Отсутствие затрат на дорогостоящие реагенты в сырье и очистку от примесей хлора отходящего углеводородного газа.
5. Количество остановов в течение 12 лет эксплуатации, а соответственно затраты на обслуживание установки, минимальны.
При переводе действующей установки изомеризации бензиновых фракций, работающей на хлорированном или сульфатированном катализаторе, на технологию Изомалк-2, возможно достигнуть снижения эксплуатационных затрат на 20-25%, повысить выход продукта.
Экологичная технология изомеризации нормального бутана в изобутан для получения высокочистого сырья химического синтеза, производства алкилата, ЭТБЭ, МТБЭ и бутилкаучука
На мировом рынке растет спрос на высокооктановый алкилат, изобутилен, ЭТБЭ, МТБЭ и бутилкаучук. Сырьем в процессе получения этих продуктов является изобутан высокой степени чистоты.
Получение изобутана путем изомеризации н-бутана по инновационной технологии Изомалк-3 на катализаторе СИ-3 — наиболее современный, эффективный и экономически выгодный способ получения сырья для этих процессов.
До недавнего времени самым распространённым в промышленности способом изомеризации нормального бутана был процесс, основанный на применении хлорированного катализатора.
При высокой степени активности и селективности, хлорированные катализаторы обладают рядом недостатков: коррозия оборудования, частая замена дорогостоящих катализаторов, токсичные отходы. Всё это приводит к повышению капитальных и эксплуатационных затрат, а следовательно, и к высокой себестоимости продукции.
Единственным альтернативным способом получения изобутана в промышленных масштабах является использование оксидного катализатора СИ-3, не содержащего хлор в качестве активного компонента.
Катализатор СИ-3 и технология его использования были разработаны в научно-исследовательской лаборатории НПП Нефтехим, а затем с успехом применены на ряде промышленных предприятий. Технология изомеризации бутана «Изомалк-3» стала продолжением серии технологий ИзомалкTM на основе катализаторов серии СИTM.
Преимущества технологии Изомалк-3
В сравнении с технологией, использующей хлорированный тип катализатора, технологию Изомалк-3 отличают следующие преимущества:
1. В технологии Изомалк-3 не применяется подача агрессивных реагентов, отсутствует коррозия технологического оборудования. Отсутствуют технологические отходы и выбросы, требующие утилизации. В продукте отсутствуют микропримеси хлора и серы.
2. Минимальные эксплуатационные затраты за счет отсутствия агрессивных реагентов, отсутствия необходимости в очистке продукта и отходящего газа от примесей хлора, длительного цикла работы и срока службы адсорбентов, минимизации количества остановов в период эксплуатации катализатора.
3. Высокая надежность каталитической системы. Временное повышение содержания примесей в сырье не приводит к безвозвратной потере активности катализатора.
4. Длительный срок службы катализатора СИ-3 — более 10 лет. Катализатор не требует перегрузок и дозагрузки в течение всего срока службы.
5. Устойчивость к действию каталитических ядов. Не требуется специальная доочистка сырья от микропримесей влаги, серы и азота. Временные изменения качества сырья не приводят к безвозвратной потере активности, в отличие от хлорированных катализаторов.
При переводе действующей установки изомеризации н-бутана, работающей на хлорированном катализаторе, на технологию Изомалк-3 будут снижены эксплуатационные затраты ориентировочно на 20%.
Способ внедрения в производство
Технология Изомалк-3 универсальна для любого нового или действующего производства:
Вариант 1. Замена хлорированного катализатора в существующей установке на катализатор СИ-3 без реконструкции. В этом случае неиспользуемое оборудование для хлорированной системы будет отсоединено, а эксплуатационные затраты на установке снизятся.
Вариант 2. Проектирование и строительство новой установки с использованием всех преимуществ технологии. Оптимальные сроки строительства — 2 года с момента начала проектирования.
Для оценки эффекта от внедрения технологии мы готовы провести бесплатную технико-экономическую оценку на вашем предприятии. Для этого, пожалуйста, свяжитесь с нами через форму обратной связи.
Сырьем установки является бутановая фракция. Реакция изомеризации протекает на катализаторе СИ-3 в присутствии водорода.
Процесс Изомалк-3 включает следующие стадии:
1) разделение на фракции изо- и нормального бутана, отделение C5+ углеводородов — проводится в блоке колонны деизобутанизации
2) подготовка сырья и водорода в адсорберах-осушителях для удаления нежелательные примесей
3) проведение реакций изомеризации бутановой фракции на катализаторе СИ-3 в одном или несколько последовательно расположенных реакторах
4) отделение растворенного водорода и легких углеводородов (С1-С3) из продукта в блоке колонны стабилизации (К-2) и направление стабилизированного продукта в блок колонны фракционирования (К-1) для получения высокочистого изобутана
Непревращенный н-бутан возвращается в реакторный блок изомеризации, тем самым обеспечивается максимальное превращение н-бутана в изо-бутан.
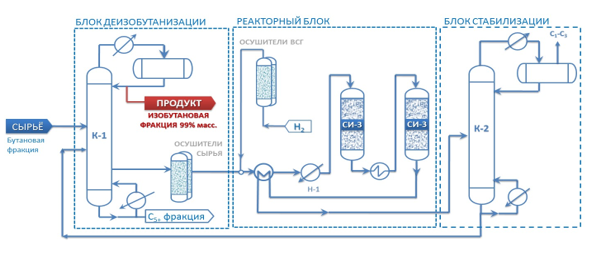
Каталитическая система технологии Изомалк-3
Преимущества катализатора СИ-3 перед хлорированными
катализаторами изомеризации бутана:
· Высокий срок службы катализатора — не менее 10 лет
· Возможность восстановления активности катализатора
· Не требуется подача хлорсодержащих соединений
· Нет защелачивания кислых газов
· Нет отходов, требующих специального обращения
· Нет примесей хлора и серы в продукте
Сочетание возможностей, которое даёт современная исследовательская лаборатория НПП Нефтехим, наличие пилотных установок и собственное катализаторное производство позволяет совершенствовать выпускаемые катализаторы с каждой новой партией.
Каждая выпускаемая партия катализаторов НПП Нефтехим проходит двойной контроль качества и пилотные испытания 24/7 непосредственно перед отгрузкой заказчику.
Качество катализатора СИ-3 подтверждено успешной многолетней эксплуатацией на промышленных установках.
Промышленное применение технологии Изомалк-3
Первая в мире установка изомеризации н-бутана по технологии
«Изомалк-3», работающая на оксидном, нехлорированном катализаторе, введена
в эксплуатацию в 2016 году в Китае и входит в состав
комплекса по получению МТБЭ, лицензиаром которого является компания Lummus.
Номинальная производительность установки по сырью (бутановой фракции) — 200 тыс. т/год.
Заказчиком проекта является Shandong Sincier Petrochemical Сo., Ltd (Китай).
Компания обратилась к технологии Изомалк-3, так как применяемый катализатор дегидрирования очень чувствителен к примесям хлора в сырье, и применение хлорированной каталитической системы было связано с высокими рисками. Проскок хлора в изобутановой фракции мог привести к останову всего комплекса. Поскольку применение катализатора СИ-3 не требует подачи хлора в сырье, то выбор был сделан в пользу технологии Изомалк-3. Проект успешно реализован и сразу после его запуска вызвал интерес других нефтеперерабатывающих компаний.
В 2017-2018 гг. в Китае были построены и запущены еще две малотоннажные установки Изомалк-3 мощностью 30 тыс. тонн в год по сырью каждая.
Позже, в 2019 году самая крупная установка Изомалк-3 была построена и введена в эксплуатацию на
НПЗ Sinopec Jinling Petrochemical (г. Нанкин, Китай), принадлежащем национальной нефтеперерабатывающей корпорации Китая.
Для переработки бутана в больших объемах требовалась эффективная и надежная технология. При этом были решены основные задачи по стабильности, экологичности и надежности процесса.
Загрузка установки по сырью реакторного блока установки составляет 480 тыс.т/год.
Технология изомеризации гептановой фракции для получения неароматического компонента автомобильного бензина с высоким октановым числом.
Прямогонная фракция углеводородов С7, выкипающая в пределах 70-105°С, состоит преимущественно из н-гептана, 2-метилгексана, 3-метилгексана и нафтеновых углеводородов. Высокое содержание неразветвлённых парафиновых углеводородов с низким октановым числом (для н-гептана оно равно нулю), делает фракцию С7 непригодной в качестве компонента современных автобензинов. Доля же изо-парафиновых углеводородов С7 с высоким октановым числом в прямогонных фракциях ничтожна мала.
Гептановая фракция не может быть эффективно переработана на существующих установках изомеризации С5-С6-фракций, поскольку катализаторы, применяемые в процессе С5-С6-изомеризации, не селективны в отношении углеводородов С7. Уровень реакций гидрокрекинга для гептанов в процессе изомеризации С5-С6-фракций достигает 50%. Кроме этого, гептаны оказывают ингибирующее воздействие на целевые реакции в процессе изомеризации С5-С6, что приводит к существенному снижению показателей всего процесса.
Направление С7-фракции в сырье установок каталитического риформинга также не является оптимальным решением при производстве бензинов. В условиях процесса риформинга со стационарным слоем катализатора скорость реакции гидрокрекинга парафиновых углеводородов С7 значительно выше скорости реакции дегидрициклизации. Вовлечение парафиновых углеводородов С7 в сырьё риформинга приводит к снижению выхода и октанового числа риформата, снижению выработки водорода и сокращению межрегенерационного периода.
Прямогонная бензиновая фракция НК-180°С содержит около 10-15% гептановой фракции, которая в процессе переработки либо разделяется между процессами изомеризации С5-С6 и риформингом, ухудшая показатели этих процессов, либо выводится отдельно без переработки.
Эффективным вариантом переработки гептановой фракции является получение высокооктанового неароматического компонента путем изомеризации по технологии Изомалк-4 с использованием катализатора СИ-4.
Внедрение технологии Изомалк-4 повышает эффективность получения автомобильных бензинов на НПЗ благодаря:
1) Увеличению количества неароматического
компонента с высоким октановым числом, вовлекаемого в производство
автобензинов, и повышению выхода автобензина на фракцию НК-180°С;
2) Возможности выполнения строгих норм по содержанию ароматики и
бензола в автобензине при одновременном уменьшении количества октаноповышающих
присадок или полном отказе от их использования;
3) Повышению срока службы катализатора риформинга за счет
исключения гептанов из сырья риформинга.
На схеме ниже показана принципиальная схема получения автомобильного бензина с включением в нее технологии Изомалк-4:
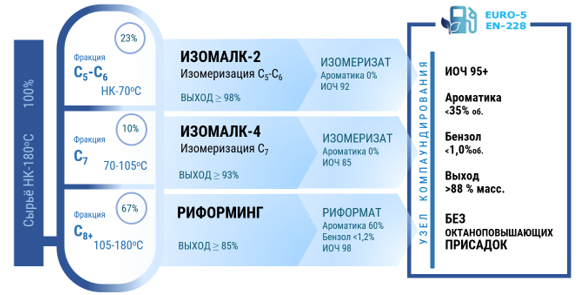
Направление гептановой фракции на изомеризацию по технологии Изомалк-4 позволяет улучшить качество и повысить объем выработки автомобильного бензина.
Каталитическая система технологии Изомалк-4
Основой технологии Изомалк-4 является уникальный
катализатор СИ-4, разработанный НПП Нефтехим.
Основные особенности катализатора СИ-4:
· обладает высокой селективностью в процессе изомеризации С7-парафинов;
· не требует подачи реагентов в процессе эксплуатации;
· обладает высокой стабильностью и устойчивостью к каталитическим ядам;
· обеспечивает проведение селективного процесса изомеризации гептанов при температурах от 160°С;
· срок службы катализатора - 10 лет;
· регенерируемый в реакторе.
Промышленное производство катализатора СИ-4 осуществляется на собственной катализаторной фабрике в г. Нижний Новгород в России. Каждая выпускаемая партия катализатора проходит многоступенчатый контроль качества.
Производство и поставка катализаторов осуществляется НПП Нефтехим с предоставлением индивидуальных гарантий на весь срок службы.
Технологическая схема установки Изомалк-4
Технология Изомалк-4 имеет аппаратное оформление, близкое к традиционной схеме Изомалк-2. Схема с рециркуляцией неразветвленных гептанов позволяет получать изомеризат с ИОЧ 83-88 из низкооктановой гептановой фракции (фракции 70-105°С).
Установка Изомалк-4 включает следующие взаимосвязанные технологические блоки оборудования:
— реакторный
блок изомеризации
(включает нагреватель сырья, непосредственно реакторы и узел осушки газа,
компрессор, сепаратор и теплообменное оборудование, возможна реализация
процесса с подачей водорода на проток);
— блок
стабилизации полученного изомеризата
для удаления углеводородного газа (С1-С4) и остатков
растворенного водорода из продукта (состоит из колонны стабилизации и
сопутствующего оборудования);
— блок колонны
деизогептанизации
служит для выделения целевого продукта – высокоразветвленных изомеров гептана,
выделения непревращенной доли гептанов и направления их в качестве рециркулята
в сырье реакторного блока с целью повышения октанового числа продукта
(состоит из ректификационной колонны и сопутствующего оборудования).
Установка Изомалк-4 не требует специальной адсорбционной очистки сырья от микропримесей серы, азота и воды. Необходимые требования по содержанию микропримесей достигаются типовой гидроочисткой сырья.
Получаемый на установке тяжёлый изомеризат, представляющий из себя концентрат нафтеновых углеводородов С7, возможно направить в сырьё установки каталитического риформинга. Это позволит улучшить показатели работы установки риформинга и получить изомеризат с более высоким октановым числом.
Особенности технологии Изомалк-4
1. Температура на входе в реакторы в процессе Изомалк-4 остаётся достаточно низкой ~160°С в течение всего межрегенерационного периода, обеспечивая необходимую глубину изомеризации
2. Устойчивость к действию каталитических ядов, не требует специальной подготовки/доочистки сырья от примесей серы и азота
3. Отсутствие затрат на дорогостоящие реагенты и очистку от примесей хлора отходящего углеводородного газа.
4. Катализатор СИ-4 регенерируемый (в реакторе) и не требует выгрузки, перезагрузки, дозагрузки в течение срока службы (10 лет).
Способы внедрения технологии в производство
Внедрение технологии Изомалк-4 не требует приобретения специального лицензированного оборудования. Простые и многократно проработанные проектные решения позволяют точно и быстро выполнить проект дооборудования с привязкой к действующему производству.
Реализация процесса возможна путем строительства новых блоков или путем модернизации старых мощностей установок риформинга, цеолитной изомеризации, хлорированной изомеризации пентан-гексановых фракций.
НПП Нефтехим обеспечивает полную техническую и консультационную поддержку проекта и гарантирует получение заявленных показателей качества продукта.