Лекция 4
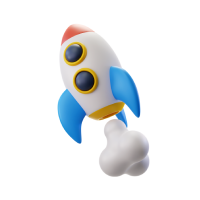
Лекция 4
1. Лекция 4. Процессы углубления переработки нефти: сравнительная характеристика существующих термических методов переработки нефти
Термохимические превращения углеводородов
При высоких температурах углеводороды нефтяного сырья подвергаются разнообразным превращениям. Это первичные реакции деструкции, приводящие к образованию продуктов с меньшей молекулярной массой, и вторичные реакции изомеризации и конденсации, в результате которых образуются продукты с той же или большей молекулярной массой.
Тип этих реакций и, следовательно, скорость, глубина и последовательность превращений зависят от стабильности углеводородов различных классов в условиях крекинга.
Мерой стабильности с достаточной степенью точности может служить величина изобарно-изотермического потенциала образования углеводородов ΔG°o6, который является функцией температуры. В таблице 1 приведены значения ΔG°об углеводородов различных классов с одинаковым числом атомов углерода и углеводородов одного класса (алканов) с различным числом атомов углерода.
Таблица 1 - Значения ∆G°об , кДж/моль углерода
При низкой температуре (298°К) углеводороды различных классов, но с одинаковым числом углеродных атомов в молекуле, по уменьшению их стабильности располагаются в ряд (ряд термической устойчивости)
CnH2n+2>∆CnH2n>CnH2n>CnH2n-6 .
Термический крекинг проводят при температуре 450 — 650 °С и давлении до 70 атм (5,0 МПа). На установках термического крекинга тяжелые нефтяные фракции под действием теплоты, но в отсутствии катализатора, разделяются на более легкие фракции.
Выход бензина при этом
процессе низкий, но в больших количествах получают средние нефтяные фракции и
устойчивое жидкое топливо.
Процесс протекает в следующей последовательности. Нефтяное сырье нагревают в
печи (см. рис. 9.6) до температуры крекинга, а полученные продукты разделяют в
ректификационной колонне.
Легкий крекинг — это мягкий термический крекинг. В результате его проведения происходит небольшое уменьшение температуры кипения, но значительно снижается вязкость. Сырье нагревают, слегка крекируют в печи, резко охлаждают легким газойлем и подвергают мгновенному испарению в нижней части фракционной колонны. Газ и бензин отводят, а более тяжелые фракции направляют на повторный цикл.
Сточные воды с установок крекинга содержат различные нефтяные фракции и могут иметь высокие значения pH, ВПК, ХПК, высокое содержание аммиака, фенола и сульфидов. На некоторых НПЗ в системах термического крекинга предусмотрены замкнутые циклы водооборота.
Назначение процесса. Термический крекинг под давлением проводят с целью получения дополнительного количества светлых нефтепродуктов, термогазойля (сырья для производства технического углерода) и дистиллятного крекинг-остатка (для производства высококачественного, анизотропного игольчатого кокса).
Параметры процесса. Процесс осуществляется под давлением от 2 до 7 МПа при температуре 480 - 540 °С. Выход светлых продуктов при крекинге остаточного сырья не превышает 30 - 35 %. Время пребывания сырья в зоне реакции — 1,5 - 2,5 мин (10 - 15 мин — в выносной камере).
Выход светлых продуктов при крекинге мазута не превышает 27 – 35 % масс. В процессе термического крекинга вакуумного газойля выход светлых нефтепродуктов может достигать 70 % масс. на сырье. При термическом крекинге ароматизированных дистиллятных продуктов (тяжелых газойлей каталитического крекинга и коксования) также достигается достаточно высокая степень превращения сырья.
Сырье и продукты. Используется остаточное (мазуты, гудроны и полугудроны — около 70 %) и дистиллятное сырье (тяжелые газойли каталитического крекинга, тяжелая смола пиролиза, экстракты селективной очистки масел и др.).
При крекинге под давлением состав газов
характеризуется значительным содержанием сухой части (метан, этан) и
умеренным
(25 - 30 %) содержанием непредельных углеводородов.
Жидким продуктам крекинга свойственно присутствие непредельных и ароматических углеводородов. При средней глубине процесса крекинг-бензины обладают невысоким октановым числом (60 - 65); с углублением процесса концентрация ароматических углеводородов возрастает, поэтому октановое число повышается: бензин, получаемый термическим риформингом лигроина, имеет октановое число 70 - 72, а у бензина, выделенного из смолы пиролиза, октановое число 80 и выше. Йодные числа типичных бензинов, образующихся при термическом крекинге под давлением и коксовании, довольно высоки (80—100 г I2 на 100 г).
С утяжелением фракционного состава продуктов
крекинга их непредельность снижается; крекинг-газойли, выкипающие в пределах
200 - 350 °С и часто используемые (после очистки) как компоненты дизельного
топлива, имеют йодное число 40 - 50
г I2 на
100 г.
Более тяжелые фракции обычно возвращают на рециркуляцию или выводят в виде
крекинг-остатка (крекинг под давлением). В зависимости от режима процесса и
качества сырья эти продукты более или менее ароматизированы. Крекинг-остатки
содержат довольно много смолисто-асфальтеновых веществ и некоторое количество
твердых частиц — карбоидов.
Типы процессов ТК. Известно несколько вариантов процесса:
§ крекинг в реакционном змеевике без выделения зоны крекинга в отдельную секцию;
§ крекинг с выносной реакционной камерой с различным уровнем жидкой фазы;
§ повторный крекинг дистиллятных продуктов или в смеси с исходным сырьем в отдельной печи;
§ крекинг с дополнительной разгонкой крекинг-остатка в вакууме.
Выбор технологической схемы процесса зависит от типа перерабатываемого сырья.
Висбрекинг
Назначение процесса. Висбрекинг — наиболее мягкая форма термического крекинга, представляет собой процесс неглубокого разложения нефтяных остатков с целью снижения вязкости остатков для получения товарного котельного топлива.
Процесс осуществляется в жидкой фазе. Возможности висбрекинга по увеличению выработки светлых нефтепродуктов ограничены требованиями к качеству получаемого остатка.
Висбрекинг может проводиться также и для производства газойля — сырья для процессов каталитического и гидрокрекинга.
Параметры процесса. Процесс осуществляют при давлении 1 - 5 МПа и температуре 430 - 500 0С.
Конверсия сырья в процессе висбрекинга в печи
невысокая (14 - 30
% исходного сырья), отбор светлых
нефтепродуктов из гудрона не превышает
5 - 20 %, а из мазута - 16 - 22 %. При
этом получается более 75 % условно непревращенного остатка — котельного
топлива.
Сырье и продукты. В качестве сырья используют мазут либо гудрон.
Получаемые продукты при висбрекинге мазута: газ, бензин, средние дистилляты, вакуумный газойль, крекинг-остаток. При висбрекинге гудрона - газ, бензин, средние дистилляты, крекинг-остаток.
Типы процессов висбрекинга. Существуют две принципиальные разновидности процесса висбрекинга:
§ печной висбрекинг - в нагревательно-реакционной печи при температуре 480 - 500 0С и времени пребывания сырья в зоне реакции 1,5 - 2,0 мин;
§ висбрекинг с выносной реакционной камерой (сокинг-камерой) - при температуре 430 - 450 0С, время реакции 10 - 15 мин. Применение сокинг-камеры повышает селективность процесса, уменьшает расход тепла (65 – 70 % количества тепла, расходуемого при печном висбрекинге), увеличивает глубину превращения сырья, снижает закоксовывание змеевика печи и увеличивает межремонтный пробег.
На современных нефтеперерабатывающих заводах висбрекинг позволяет:
§ сократить производство тяжелого котельного топлива;
§ уменьшить количество прямогонных дистиллятов для разбавления тяжелых, высоковязких остатков (гудронов), используемых в качестве котельного топлива;
§ расширить ресурсы сырья для каталитического крекинга и гидрокрекинга;
§ выработать дополнительное количество легких и средних дистиллятов, используемых как компоненты моторных и печных топлив.
Коксование
Назначение процесса. Коксование — одна из наиболее жестких форм термического крекинга нефтяных остатков с целью получения дополнительного количества светлых нефтепродуктов и нефтяного кокса. Процесс проводят в направлении концентрирования асфальто-смолистых веществ сырья в твердом продукте-коксе и получения в результате этого более богатых водородом продуктов — бензина и средних дистиллятов.
Параметры процесса. Осуществляется при низком давлении и температуре 480 - 560 0С.
Сырье и продукты. В качестве сырья используют тяжелые нефтяные остатки и кубовые остатки различных производств: гудроны, мазуты, смолы пиролиза, крекинг-остатки. За рубежом используют также каменноугольные пеки и сланцевые смолы, тяжелые нефти из битуминозных пород и др.
Опасность закоксовывания реакционной аппаратуры зависит от качества исходного сырья, прежде всего от его агрегативной устойчивости. Тяжелое сырье, богатое асфальтенами, но с низким содержанием полициклических ароматических углеводородов, характеризуется низкой агрегативной устойчивостью, и оно быстро расслаивается в змеевиках печи, что является причиной коксоотложения и прогара труб. Для повышения устойчивости сырья к сырью добавляют ароматические концентраты, такие как экстракты масляного производства, тяжелые газойли каталитического крекинга, тяжелая смола пиролиза и др.
В зависимости от назначения к нефтяным коксам предъявляют различные требования. Основные показатели качества коксов:
· содержание серы (малосернистые (до 1 % S), среднесернистые (до 1,5 % S), сернистые (до 4 % S) и высокосернистые (выше 4,0 % S));
· золы (малозольные (до 0,5 %), среднезольные (0,5—0,8 %) и высокозольные (более 0,8 %));
§ летучих компонентов (кусковой (фракция с размером кусков свыше 25 мм), «орешек» (фракция 8—25 мм) и мелочь (менее 8 мм));
§ гранулометрический состав;
§ пористость;
§ истинная плотность;
§ механическая прочность;
§ микроструктура и др.
Получаемые при коксовании жидкие дистилляты имеют невысокие эксплуатационные показатели (из-за повышенного содержания в них непредельных и сернистых соединений) и требуют дальнейшей термогидрокаталитической обработки для вхождения в состав товарных топлив.
Наличие в газе непредельных углеводородов создает предпосылки для его использования (после соответствующего фракционирования) в процессах алкилирования, полимеризации и др.
Типы процесса коксования. Промышленный способ коксования осуществляют на установках трех типов:
§ периодического коксования (периодические подача сырья и выгрузка продуктов) в кубах;
§ полунепрерывного или замедленного коксования (непрерывная подача сырья и периодическая выгрузка продукта) в камерах (барабанах);
§ непрерывного коксования (непрерывные подача сырья и выгрузка продуктов) в псевдоожиженном слое кокса-носителя.
Периодическое коксование осуществляется в обогреваемых камерах (периодического действия) для переработки нефтяного сырья с целью получения электродного кокса специального назначения. Процесс отличается низкой производительностью и большой трудоемкостью обслуживания коксовых кубов. Максимальный выход кокса достигает 50 % масс. на сырье (выход светлых нефтепродуктов невысокий — до 25 % масс. на сырье).
Замедленное (полунепрерывное) коксование проводится в необогреваемых камерах и применяется для переработки нефтяных остатков в светлые нефтепродукты, газойлевые фракции и кокс.
При переработке малосернистого сырья, а также при использовании термостойкого и ароматизированного сырья (дистиллятного крекинг-остатка термического крекинга вакуумного газойля, тяжелых газойлей каталитического крекинга и коксования) стремятся к получению максимального количества высококачественного кокса. При замедленном (полунепрерывном) коксовании из гудрона малосернистых нефтей получают до 25 % электродного кокса, а из дистиллятного крекинг-остатка — около 38 % электродного игольчатого кокса. При переработке сернистого сырья процесс проводят в направлении получения максимального количества жидких продуктов. Выход светлых нефтепродуктов из гудрона сернистых нефтей достигает 47 % масс. на сырье, в том числе легкого газойля (180 - 350°С) — 35 % масс.
Непрерывное коксование (термоконтактный крекинг) применяется для переработки тяжелых видов сырья, в том числе битуминозных нефтей с высоким содержанием металлов и высокой коксуемостью.
Процесс осуществляется в присутствии порошкообразного коксового теплоносителя. В реакторе сырье коксуется на поверхности теплоносителя, нагретого до 600 °С. Порошкообразный кокс может быть реализован как товарный продукт (выход на сырье при переработке гудрона около 20 % масс.) или подвергнут парокислородной газификации с образованием низкокалорийного топливного газа.
При термоконтактном крекинге с газификацией образующегося кокса достигается максимальная (из рассматриваемых процессов) степень конверсии сырья в газообразные и жидкие продукты с выходом до 99 % масс. на сырье.
Пиролиз углеводородного сырья
Назначение процесса. Пиролиз углеводородного сырья — самая жесткая форма термического крекинга с целью получения углеводородного газа, обогащенного непредельными углеводородами.
Пиролиз — базовый процесс нефтехимии, на его основе получают около 75 % нефтехимических продуктов.
Параметры процесса. К основным факторам процесса относятся температура и длительность реакции (причем каждой температуре соответствует оптимальное время контакта). Для сравнительной оценки режимов пиролиза жидкого сырья и его термической стабильности используют фактор жесткости:
,
(1.1)
где t — температура, 0С; т — время контакта, с.
Процесс осуществляют при 700 - 900 0С, время контакта 0,25 - 0,40 с. Регулировкой режима может быть достигнут максимальный выход либо этилена, либо пропилена, либо бутиленов и бутадиена. Наряду с газом образуется жидкий продукт — смола, содержащая как моно-, так и полиароматические углеводороды. С утяжелением сырья возрастает выход смолы.
Иногда вместо фактора жесткости используют значение атомного отношения Н/С в жидких продуктах пиролиза. Чем жестче режим процесса, тем ниже это значение.
Для каждого вида сырья существует оптимальное сочетание температуры и продолжительности пиролиза.
Значительное газообразование при пиролизе жидкого сырья и получение более легких, чем сырье, компонентов при пиролизе газообразного сырья вызывают большое увеличение (обычно в 1,5 - 2 раза) удельного объема паровой (газовой) фазы. Известно, что реакциям, протекающим с увеличением объема, способствует низкое давление в реакционной зоне или, что то же самое, низкое парциальное давление продуктов. Для уменьшения роли реакций уплотнения пиролиз ведут при максимально низком давлении (обычно на выходе из печи давление равно 0,2—0,25 МПа).
Сырье и продукты. Основное сырье процесса при получении низших олефинов — попутные газы нефтедобычи и технологические газы процессов нефтепереработки, газовые бензины, прямогонные бензины, рафинат риформинга и др. В последнее время в качестве сырья пиролиза используют все более тяжелые углеводородные смеси.
Основное направление использования жидких продуктов пиролиза — получение бензола и других ароматических углеводородов, нефтеполимерных смол, сырья для производства технического углерода.
Около трети общей выработки дистиллятных жидких продуктов пиролиза используется как компонент автобензина.
Деасфальтизации нефтяных остатков
Тяжелые нефтяные остатки (гудроны, полугудроны, битумы) можно отнести к коллоидным системам, в которых в качестве дисперсной фазы выступают асфальтены с адсорбированными на них смолами, а в качестве дисперсионной среды – масла и растворимые в них смолы.
Сами по себе тяжелые нефтяные остатки можно отнести к стойким лиофильным коллоидам, не способным к самопроизвольной коагуляции асфальтенов. Устойчивость коллоидного состояния зависит от природы асфальтенов и их концентрации в сырье, от природы масел и смол и от концентрации их в остатке. Агрегативная устойчивость высокомолекулярных коллоидных систем связана с явлением сольватации, а именно: с образованием на поверхности тонкодиспергированных асфальтенов, сольватных оболочек из смолистых веществ и полициклических ароматических углеводородов. От степени диспергации асфальтенов и от толщины сольватной оболочки зависит устойчивость систем. Углеводороды парафинового ряда обладают свойством разрушать сольватную структуру тяжелых остатков, что ведет к укрупнению частиц асфальтенов с последующей их коагуляцией из коллоидного раствора. При удалении из остатка парафиновой углеводородной фракции самопроизвольно начинается обратный процесс – пептизации асфальтенов. Таким образом, степень лиофильности и лиофобности системы возможно регулировать введением в остаток парафиновых углеводородов. С позиции теории коагуляции легко объяснить многие закономерности процесса. Так, например, более низкую глубину деасфальтизации при применении в качестве растворителя пропан-пропиленовой фракции (вместо пропана) объясняют более высокой пептизирующей способностью по отношению к асфальтенам пропиленовой части растворителя. Переход в коагулят вместе с асфальтенами значительного количества масляных фракций объясняют высокой адсорбционной способностью асфальтенов. Известное повышение глубины деасфальтизации с повышением температуры объясняют усилением лиофобности асфальто-смолистых веществ (АСВ) по отношению к осаждающим растворителям. С повышением температуры процесса область концентраций масло – асфальт, при которых жидкость разделяется на две фазы, расширяется. Иными словами, при высоких разбавлениях пропаном сырья повышение температуры приводит к смещению фазового равновесия системы и способствует переходу масел из пропановой в асфальтовую фазу.